OPT是一种改善生产管理的技术,以色列物理学家Eli Goldratt博士于70年代提出,用于安排企业生产人力和物料调度的计划方法。最初被称作最佳生产时间表,80年代才改称为最佳生产技术。后来Goldratt又进一步将它发展成为约束理论。OPT的倡导者强调,任何企业的真正目标是现在和未来都赚钱;要实现这个目标,必须在增加产销率的同时,减少库存和营运费用。
它吸收MRP和JIT的长处,是以相应的管理原理和软件系统为支柱,以增加产销率、减少库存和运行为目标的优化生产管理技术。其特别之处不仅在于提供了一种新的管理思想,而且在于它的软件系统。OPT两大支柱是OPT原理及OPT软件。
它是一套可提高产出、减少存货的分析性技术理论。OPT系统将重点放在控制整体产出的瓶颈资源上,优先处理所有瓶颈作业,并以平衡物料流动为原则,使整个系统达到产出最大的目的。
OPT的基本内容
OPT其指导思想实质上是集中精力优先解决主要矛盾,这对于单件小批生产类型比较适应。这类企业由于产品种类多、产品结构复杂,控制对象过多,因此必须分清主次,抓住关键环节。其基本内容包括以下四方面:
1) 物流平衡是企业制造过程的关键
对企业的产品需求是外部因素,时刻都在变化。为适应市场,企业必须以可能的低成本、短周期生产出顾客需要的产品。因此,制造问题主要是物流平衡问题,即需要强调实现物流的同步化。
2) 瓶颈资源是产品制造的关键制约因素
在制造过程中,影响生产进度的是瓶颈环节。瓶颈资源实现满负荷运转,是保证企业物流平衡的基础。瓶颈资源损失或浪费1小时,制造系统即损失或浪费1小时。 因此,瓶颈资源是制造系统控制的重点,为使其达到最大的产出量可采取以下措施:
在瓶颈工序前,设置质量检查点,避免瓶颈资源做无效劳动。
在瓶颈工序前,设置缓冲环节,使其不受前面工序生产率波动影响。
采用动态的加工批量和搬运批量。对瓶颈资源,通常加工批量较大,减少瓶颈资源的装设时间和次数,提高其利用率;而较小的运输批量,使工件分批到达瓶颈资源,可减少工件在工序前的等待时间,减少在制品库存。
3)由瓶颈资源的能力决定制造系统其他环节的利用率和生产效率。
4)对瓶颈工序的前导和后续工序采用不同的计划方法,提高计划的可执行性。
根据OPT的原理,企业在生产计划编制过程中,首先应编制产品关键件的生产计划,在确认关键件的生产进度的前提下,再编制非关键件的生产计划。
OPT的主要概念
识别约束
识别企业的真正约束所在是控制物流的关键。一般来说,当需求超过能力时,排队最长的机器就是 “瓶颈”。
瓶颈约束整个系统的出产计划
产品出产计划的建立,应该使受瓶颈约束的物流达到最优。一般按有限能力,用顺排方法对关键资源排序。为了充分利用瓶颈的能力,在瓶颈上可采用扩大批量的方法,以减少调整准备时间,提高瓶颈资源的有效工作时间。
“缓冲器”的管理。其目的是防止系统内外的随机波动造成瓶颈出现等待任务的情况。一般要设置一定的“库存缓冲”或“时间缓冲”。
控制进入非瓶颈的物料。进入系统非瓶颈的物料应与瓶颈的产出率同步。一般是按无限能力,用倒排方法对非关键资源排序。非关键资源上排序的目标是使之与关键资源上的工序同步。倒排时,采用的提前期可以随批量变化,批量也可按情况分解。
OPT的生产排序原则
OPT管理思想具体体现在生产排序原则上。有九条原则是实施OPT的基石。这些原则独立于软件之外,直接用于指导实际的生产管理活动。OPT有关生产计划与控制的算法和软件按照这九条原则提出和开发的:
1. 重要的是平衡物流,不是平衡能力。物流平衡使各个工序与瓶颈同步,能力平衡是生产能力充分开动;
2. 制造系统的资源可分为瓶颈和非瓶颈两种。非瓶颈资源的利用率是由系统的其它约束条件决定的,而不是由其本身能力决定的;只有瓶颈制约着系统的产销率。
3. 资源“利用”和“开动”不是同义的;应该反对盲目的使所有的机器或工人忙起来。
4. 瓶颈资源损失一小时相当于整个系统损失一小时,而且是无法补救的。重点应该抓提高瓶颈的利用率。
5. 想方设法在非瓶颈资源上节约时间以提高生产率只是一种幻想,非瓶颈资源不应满负荷工作。
6. 产销率和库存量是由瓶颈资源决定的。为保证瓶颈资源负荷饱满并保证企业的产出,在瓶颈工序和总装配线前应有供缓冲用的物料储备。瓶颈工序前可用拉式作业,其后可用推式作业。
7. 转移批量可以不等于甚至多数情况是不应等于加工批量。
8. 加工批量是可变的,而不是固定不变的。每个工序的批量按实际情况是动态决定。
9. 提前期应该是可变的而不是固定的。考虑到系统所有的约束条件后才能决定计划进度的优先级。提前期只是排进度的结果。
OPT的计划与控制系统又称为DBR系统
OPT的发展
最优生产技术OPT的管理哲理向许多传统的管理思想发出挑战,从而拉开了论战的序幕。高德拉特的合伙人之一Robert E. Fox曾经以 “OPT, MRP or JIT—What’s Best?” 为题,将OPT作为一种计划方法向MRP的霸主地位提出挑战,并在APICS协会引起很大轰动。随后,制造业社会试图要求高德拉特公开OPT软件的“黑箱”算法逻辑,又引起了论战。关于OPT的最后论战是由Eli Goldratt and George Plossl 在1984年APICS的国际会议上顶着巨大压力发布白皮书“A Town Without Walls”引起的,这篇文章间接批评了APICS的领导层。
实施OPT的要求及条件
对OPT,目前理论界的认识还不一致,存在着各种看法,主要包括:
①把OPT当做一种新的计划思想;
②作为一种作业计划的仿真语言;
③作为生成MPS、物料和能力需求计划及详细计划的一个软件包;
④作为一种处理数据精确度的一种尝试,以求在数据未达到高度精确之前获得利润。
但有一点很明显,即OPT强调的是车间现场,其着眼点在于企业车间现场的一些决策量上,并据此来实现对生产的计划与控制。其做法的基本点是使用一些重要的判定准则来决定每一作业的先后顺序,即使用一组“管理系数”的加权函数,来确定每个作业的优先权数及批量,制定出一个合理的生产计划。这些管理系数涉及到理想的产品组合、交货期、理想的 安全库存水平以及瓶颈资源的使用等等。
OPT实施的关键是制定计划后的落实工作。在落实计划过程中,传统的许多做法是有害的,其中最大的威胁将来自传统的成本会计的考核体系。因为成本会计体系忽视了瓶颈与非瓶颈的区别,其考核一般是通过设备和操作工人的利用率及生产成本,而不是通过整个系统的有效性来进行的,它着重于局部的优化,这必然助长了 人们盲目生产的作法,其结果是无论对瓶颈资源还是对非瓶颈资源都力求充分地使用。人们为了完成工时和设备利用率会盲目生产,最终必然导致高库存和浪费。针对这些情况,OPT则力求从全局的观点来进行考核,从原材料的采购一直追踪到产品销售。其考核体系对瓶颈与非瓶颈是分别对待的,认为对非瓶颈的考核不应以 生产量为依据,而应以它生产的有效的产品量来考核。按OPT观点,成本会计注重的是“活力”而非”利用”,而正确的做法应该是注重“利用”而非“活力”。
另外,OPT软件的具体运行和MRP一样需要大量的数据支持,例如产品结构文件、加工工艺文件以及精确的加工时间、调整准备时间、最小批量、最大库存、替代设备等等数据。同时要成功地实施OPT,还要求管理者必须对OPT产生的计划要有信心,要改变一些旧的作业方式,例如接受午餐和工修连续工作制的作法等。
从OPT的实践表明,它比较适合于一些基本、简单的产品及很大的批量且所需工序较少的情况,而在单件生产车间中发挥的效果不佳。其适用条件为,①瓶颈要相对稳定;②瓶颈要保证达到100%的负荷能力;③需求是相对稳定的;④员工愿意而且能够服从计划的调度安排。
再者,OPT对于动态的数据以及瓶颈和接近瓶颈资源的数据要求精确。实现OPT还需对员工进行培训,使他们能在不同的生产岗位上及时发现问题,跟踪问题,最终用OPT方法来解决问题。
OPT案例分析 ">编辑] 案例一:基于OPT的ERP作业计划编制方法的分析
一、基于OPT的ERP作业计划编制方法的逻辑图
图给出了基于OPT的ERP作业计划编制方法的逻辑图,其主要环节的处理内容如下:
作业任务
即需要进行作业计划编制的各作业任务 本文不将作业计划编制作为一个单独的系统 而是从系统集成角度出发 根据 ,ERP处理逻辑 由物料需求计划子系统依据工艺路线产品结构生成作业任务
作业计划预编制
为了简化整个作业计划编制过程 我们将作业计划分成作业计划预编制 基于调度原则的作业计划编制两个过程 作业计划预编制是针对作业任务较少 工作中心较多的情况 工作中心上可能不会出现多个加工任务 这样只需采用简单的倒排或顺排即可 不必考虑同一工作中心上作业调度原则
冲突判断
冲突判断是指判断作业任务所涉及的每个工作中心是否出现多个作业同时加工的情况 如不出现冲突 则经过作业计划预编制生成的作业计划即可作为正式的作业计划,如出现冲突! 则进行基于调度原则的作业计划编制过程,该过程分关键作业编制、非关键作业编制两部分。
关键作业计划编制。
首先,根据调度原则计算出关键工序的开工时间、完工时间。然后,对位于关键工序前面的工序, 以关键工序为基准, 按拉动式计划原则,由后往前倒排, 计算出各工序的开工时间、完工时间;对位于关键工序后面的工序,以推动式计划原则, 由前往后顺排。
非关键作业计划编制
根据调度原则计算出各工序的开工时间、完工时间。
作业反馈
通过对已编制好的作业计划的完工情况进行跟踪, 计算出各物料的工艺路线的动态提前期$ 工作中心的动态能力等, 并对工艺路线和工作中心定义中的参数进行动态更新、调整,从而形成一个能反映客观变化的反馈机制!并实现工艺路线与作业计划的有机集成。
工艺路线
对各自制件定义了各工序的工序名称、对应工作中心、所需的准备时间、加工时间、转移时间等信息,其中有关时间的参数是由作业进度反馈动态确定的。
调度库
调度库中主要存放作业调度规则、倒排及顺排的原则,以及能力资源不足时采取的措施,如增加人力、外协等。
二、作业计划预编制
作业计划预编制的编制过程如下:
1.物料需求计划根据物料清单及产品的交货日期生成建议的加工单;
2.订单经确认后下达,系统同时生成该加工单的加工工艺路线文件,包括加工单号、物料代码、工序号、订单数、完工数、开工日期、完工日期等信息;
3.根据加工单工艺路线并结合工作中心能力进行车间作业计划编制!本文采用倒排方法,从最后一道工序一直往前排,具体算法描述如下:
已知MRP运行得到各加工件建议开工时及完工时间,工件数n,第i加工件具有m道工序。
求解各加工件的开工时间和完工时。
推导i从第
式中、、、、分别为该工序的排队时间、准备时间、加工时间、等待时间和传送时间;Q_i为加工数量。
经过作业计划预编制,通常出现如下几种情况:
1.各工作中心上没有任务冲突,作业计划预编制得到的结果可作为正式作业计划下达;
2.计算结果表明该工件可能拖期,常采用转移部分工作到替代工作中心上等措施;
3.关键工作中心的能力严重冲突,只能根据企业实际情况!采用相应的调度原则,如先满足关键作业的安排,或采用外协等措施。
结合OPT和ERP各自在作业编制上的特长,采用ERP作业计划编制使用的能力-负荷图,形象地确定关键工作中心的能力状况,从而确定作业计划的瓶颈所在!如果工作中心由多台相同工作能力的设备所组成,则将工作中心任务进行分解,细化到各设备。最后按OPT思想以关键工序为基础对前后工序进行拉式、推式的作业计划编制。
三、关键工作中心任务分解
当关键工作中心负荷超过其能力时,可将工作中心上的任务按作业数分解到各加工设备上,下图用能力+负荷图。描述了该分解过程,该工作中心由 K台相同能力的设备组成,现将该工作中心上的任务合理地细分到设备上。整个任务分解可用如下数学公式进行描述:
已知经作业计划预编制得到各加工件的开工日期、完工日期,在时间段内关键工作中心能力发生冲突,该工作中心由M台相同工作能力的设备所组成,其累积能力为,其负荷为。
求解工作中心分解出m台设备加工其中k个加工件,另外的M-m台设备加工剩余的加工件。
推导 从数学角度讲,上述工作中心的分解问题不是一个唯一解,但结合企业实际情况!可根据加工件的缓急程度,必须先确保若干个加工件的正常交货,这里设为k从而得出相应所需投入的设备数m。投入的m台设备的能力尽可能接近k个加工件所需的负荷:
上述公式可求解出&投入m台设备就可以满足k个加工件在的正常生产,与此同时它们在该工序的开工时间、完工时间为。
当m=M时,表示时间段内该工作中心所有设备均在加工上述k个加工件!因此剩下的K-k个加工件的完工时间T_F可根据下式计算得到:
=
当m<M时,剩下的K-K个加工件则在M-m台设备上进行加工,当k个加工件在T2完成后,即可投入K-k个加工件的生产,因此剩余加工件的完工时间TF可以由下式计算得到:
四、关键工序前后工序的作业计划编制
关键工序的开工时间和完工时间由式-式得到后,根据/OPT思想,以关键工序为基准,分别采用不同的策略计算出前后工序。关键工序之前的工序采用拉动式原则,由后往前倒排,即
关键工序之后的工序采用推动式原则,由前往后顺排,即
五、以OPT思想为核心的作业计划编制
整个编制过程如图所示,具体描述如下:
1)读取经过作业计划预编制生成的各物料的计划编制结果;
2)如果所有工作中心没有任务冲突,则预编制作业计划即为最终的作业计划;
3)如果工作中心任务发生冲突,读取对应工作中心的能力信息和设备的数量;
4)确定关键物料及对应关键工序,将生产中负荷重#能力紧的工作中心定义为关键工作中心;
5)对关键工作中心进行任务分解,对关键物料按式计算关键工序的开工时间#完工时间,对非关键物料按式式、计算关键工序的开工时间、完工时间;
6)对位于关键工序前面的工序,按拉动式计划原则,按式式由后往前倒排,即前道工序的完工时间等于后道工序的开工时间,以关键工序的开工时间作为递推的基准;
7)对位于关键工序后面的工序,按推动式计划原则,、式由前向后顺排,即后道工序的开工时间等于前道工序的完工时间,以关键工序的完工时间作为递推的基准。
外部链接 了解关于OPT及TOC的更多信息 参考文献
- ↑ 朱华锋,谭建荣,李涛.基于最优生产技术的ERP作业计划编制方法的研究.中国机械工程,2005,16
- ↑ Wiendahl H.面向负荷的生产控制.肖田元译.北京:清华大学出版社.1999
深圳投融网商务有限公司是一家专注企业投融资与上市服务的专业机构。公司团队来自国内外的投行精英,具备丰富的国内外的投资银行从业经验,拥有丰富的金融、财务、管理、审计、法律等专业知识与上市辅导经验。
投融网(www.ipo.hk)创建于2011年,拥有300万+俱乐部成员,涵盖银行、券商、信托、政府平台公司、上市公司、拟上市公司、融资租赁公司、商业保理公司、公募基金、私募基金、风险投资机构、天使投资机构、律师事务所、会计师事务所、评估机构、新闻媒体、高净值个人投资者等。秉承链接、赋能、共赢的经营理念,构建了高效的投融资与上市服务生态圈。
欢迎各类机构洽谈合作。
邮箱:service@ipo.hk
电话:0755-33572246

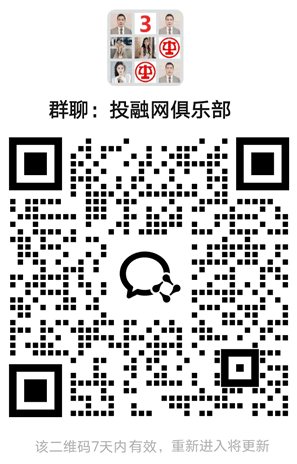